What are the precautions for the cold heading process of fasteners
Apr 22,2024
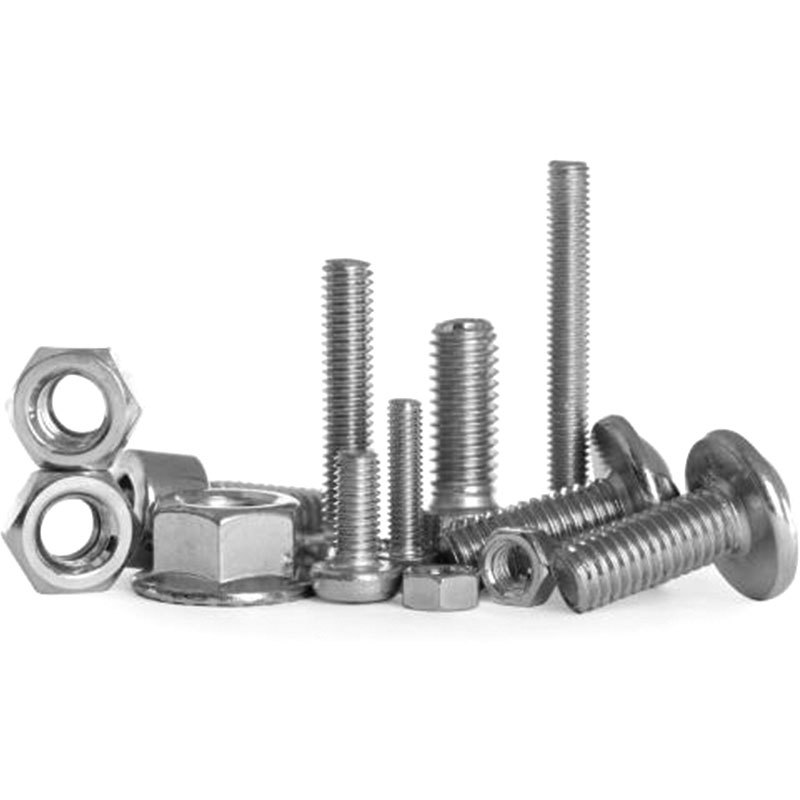
Cold heading is widely used in various industrial sectors such as aviation, aerospace, and automobiles, mainly for the processing technology of fasteners such as bolts, bolts, screws, nuts, etc. It has the characteristics of smooth operation, high accuracy, high production rate, and easy automation. The multi station automatic cold heading machine adopts a cold heading method to feed the disc element or bar material through roller drive, sequentially feed, cut, press the ball, press the angle, punch, and complete several processes in one machine. The cold heading station is arranged horizontally and has the characteristics of accurate positioning, stable operation, and convenient maintenance. Below, we will briefly introduce the precautions for processing fasteners using cold heading technology:
1、 Performance requirements for various components of multi station cold heading machines
(1) The connection between the crankshaft and the body, as well as the impact connecting rod, is made of high wear-resistant alloy copper tiles, which have a large bearing capacity, long service life, and low maintenance costs.
(2) The body is made of cast ductile iron with added alloy, which has high tensile strength and good wear resistance.
(3) Adopting a two-stage gear transmission system, with high transmission efficiency and large transmission torque.
(4) Equipped with pneumatic clutch brakes to reduce motor power and energy consumption.
(5) The cutting system adopts a guide plate to drive the cutting rod, which moves back and forth, and the cutting force is transmitted in a straight line. The force is large, stable, and has good dynamic balance.
(6) The clamp system can be flipped or translated. Facilitating the arrangement of forming processes.
(7) Equipped with a frequency conversion speed regulation device, it can achieve stepless speed regulation within a certain range.
(8) Equipped with fault detectors and safety protection devices, the equipment will automatically shut down in case of equipment failure, providing protection for the equipment and molds.
(9) Install a thrust device on the feeding box to improve feeding accuracy.
(10) The lubrication system has a simple and efficient oil circuit design, which can effectively protect the punching rod and workpiece while ensuring circulation filtration.
2、 Selection of raw materials for workpieces
(1) The raw materials must undergo spheroidization annealing treatment, and their metallographic structure is spherical pearlite.
(2) In order to minimize the tendency of material cracking and improve the service life of the mold, it is also necessary to ensure that the cold drawn material has the lowest possible hardness to improve plasticity.
(3) The precision of raw materials should generally be determined based on the specific requirements and process conditions of the product. Multi station cold heading machines generally have lower requirements for the precision of reduced diameter and strong shrinkage dimensions.
(4) The surface quality of raw materials requires a lubricating film with a dull dark color, and the surface must not have defects such as scratches, folds, cracks, burrs, rust, oxide skin, pits, and pits.
(5) The total thickness of the decarburization layer in the radial direction of the raw material is required to not exceed 1% of the diameter of the raw material.
(6) To ensure the cutting quality during cold forming, it is required that the raw materials have a hard surface and a soft core.
(7) The raw materials should undergo cold heading tests, as cold work hardening increases the deformation resistance. The lower the sensitivity of the material to cold work hardening, the better.
Contact Us
E-mail:
Phone/WhatsApp:
Address:
East of Dongmingyang Village,Linmingguan Town,Yongnian District,Handan City,Hebei Province